top of page

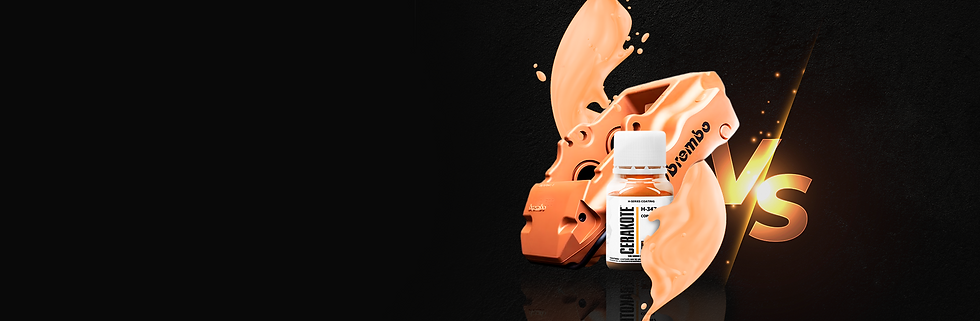
VEJA A
APLICAÇÃO NV EM AÇÃO
Diversos testes entre a pintura em Cerakote® e acabamentos concorrentes foram realizados para mostrar na prática qual é a melhor opção do mercado. Conferir a seguir cada teste e seus resultados, e tire suas próprias conclusões.
APLICAÇÃO NV
VS.
ANODIZAÇÃO
Quando se trata de proteção contra corrosão, a melhor opção é evidente. Veja a seguir quem se sai melhor nessa competição de resistência e durabilidade. Os atributos que serão analisados a seguir são as opções de cores e aplicações, a consistência das cores, o impacto da aplicação nas ligas de alumínio e, por fim, o impacto ambiental de cada um.
OPÇÕES DE CORES E APLICAÇÕES
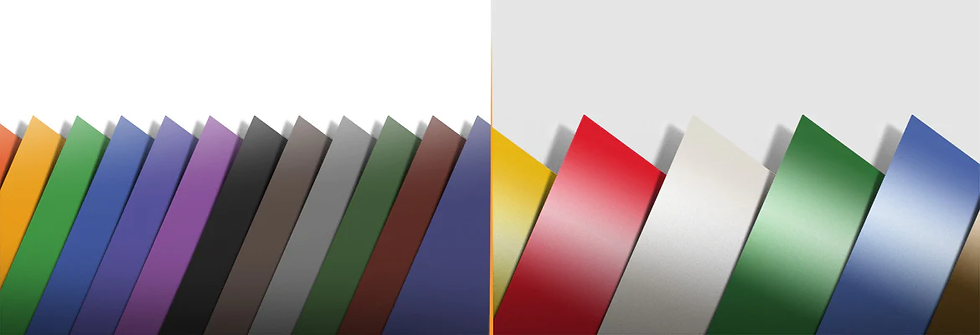
Cerakote®
Anodização
A Cerakote® oferece mais de 200 cores exclusivas e populares e pode ser aplicada a todos os metais ferrosos e não ferrosos, plásticos, compostos e muitos outros substratos, o que a torna um revestimento universal como alternativa à anodização.
Devido aos produtos químicos usados no processo, a anodização oferece uma seleção de cores muito limitada e só pode ser usada em superfícies de alumínio e titânio.
CONSISTÊNCIA DE CORES

Cerakote®
Anodização
Todas as cores Cerakote são mantidas em um padrão de consistência de cor de um Delta E de 1 ou menos.
Normalmente, o olho humano só consegue ver diferenças de variação de cor superiores a um Delta E de 2 ou mais, o que torna a Cerakote a substituição perfeita da anodização para acabamentos de alto volume.
A consistência da cor é conhecida por variar amplamente de peça para peça e de lote para lote devido a variações químicas e diferenças sutis no substrato que não podem ser controladas.
IMPACTO NAS LIGAS DE ALUMÍNIO

Cerakote®
Anodização
O Cerakote NÃO afeta negativamente as propriedades de fadiga das ligas de alumínio.
O processo de anodização cria uma camada de óxido frágil e porosa, e tensão residual de tração, o que afeta negativamente as propriedades de fadiga das ligas de alumínio. Essa fadiga foi amplamente relatada e documentada.
IMPACTO AMBIENTAL

Cerakote®
Anodização
A Cerakote não contém metais pesados e é um revestimento compatível com REACH, ROHS e Prop 65.
O processo de anodização com ácido crômico libera cromo hexavalente, um poderoso carcinógeno, no meio ambiente. Como resultado, o uso do cromo hexavalente está se tornando cada vez mais restrito pelas regulamentações.
As empresas escolhem a nossa aplicação por sua durabilidade, consistência, seleção de cores e melhor tempo de resposta.
A Cerakote® pode ser aplicada em qualquer lugar do mundo, o que a torna um revestimento seguro e acessível para qualquer aplicação.
Garanta a melhor proteção do mercado para suas peças!
APLICAÇÃO NV
VS.
CORROSÃO
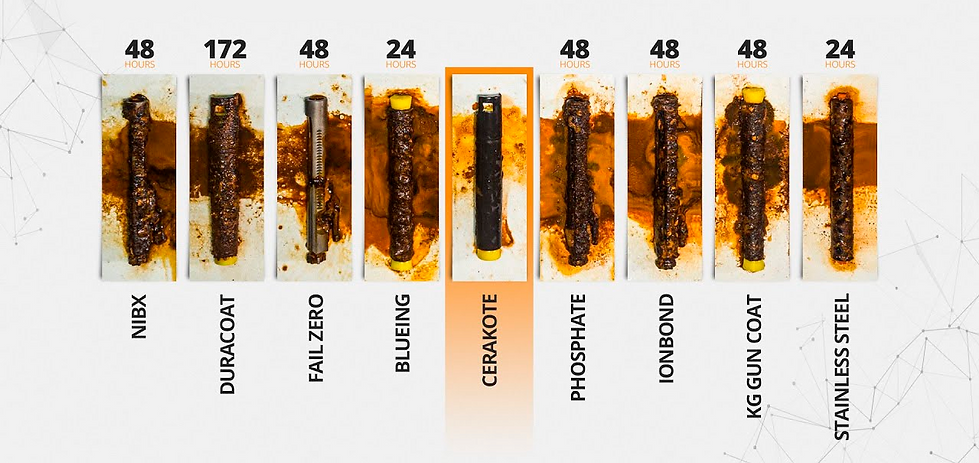
Quando se fala em acabamentos de peças de aço em geral, a atenção é voltada para fatores importantes de desempenho, como:
Dureza
Resistência química
Lubricidade
Resistência à abrasão
Cor
Mas nenhum desses aspectos é tão importante quanto a proteção contra corrosão. Para eleger a melhor opção de acabamento do mercado, foi realizado um teste de câmara de sal entre a Cerakote® e sete acabamentos concorrentes. Quem irá apresentar o acabamento mais eficiente?

O TESTE

Os testes foram feitos de acordo com as normas ASTM. De acordo com a ASTM B117-03, o teste de corrosão fornece um ambiente corrosivo ajustado para 35°C e uma concentração de 5% de sal. Dentro de uma câmara, foram colocadas peças semelhantes, cada uma contendo um dos acabamentos concorrentes da Cerakote®: bluing, FailZero, NIBX, Ionbond, Phosphate, KG Gun Kote e por fim, Duracoat®. Para fins de comparação, uma barra de aço inoxidável também foi submetida ao teste, sendo 9 peças testadas no total.
Para testar a durabilidade e resistência de cada acabamento a corrosão, a câmara controlada de sal foi ligada e só seria desligada quando todas as peças apresentassem sinais de corrosão.

O RESULTADO
O teste foi concluído após 2.034 horas de duração, quando o Cerakote® finalmente mostrou os primeiros sinais de corrosão. De acordo com a norma de testes ASTM B117-03, a aplicação que oferecemos terminou em disparada na frente, durando 11 vezes mais que o acabamento concorrente mais próximo e 85 vezes mais que o bluing ou o aço inoxidável.

Veja como ficou o ranking de resistência:
· O bluing e o aço inoxidável apresentaram sinais visíveis de corrosão nas primeiras 24 horas.
· A corrosão foi visível nas primeiras 48 horas no FailZero, NIBX, Ionbond, Phosphate e KG Gun Kote.
· Em 172 horas, o Duracoat® começou a mostrar sinais de corrosão.
· Finalmente, o teste foi concluído em 2.034 horas, quando o Cerakote mostrou os primeiros sinais de corrosão.
Garanta a melhor proteção do mercado para suas peças!
APLICAÇÃO NV
VS.
TEFLON®
E XYLAN®
Em ambientes costeiros a preservação contra corrosão e o desempenho são cruciais para elementos como fixadores, parafusos, roscas, entre outros. Além da necessidade de baixo atrito nessas aplicações, a proteção contra corrosão é igualmente vital. Reconhecendo a Cerakote como uma alternativa ou substituto eficaz para os revestimentos de PTFE, foram realizados testes a fim de ter uma comparação direta com outros revestimentos convencionais da indústria.
O TESTE

O revestimento Cerakote E-100 Blackout foi submetido a testes de resistência à corrosão em confronto com os revestimentos Teflon® Black 958G, Teflon® Metallic Black 420G e Xylan® 142X, comumente empregados em aplicações marítimas para prevenir a corrosão. Todos os revestimentos foram aplicados em parafusos de aço simples e porcas zincadas para intensificar a taxa de corrosão galvânica.
A avaliação foi conduzida em uma câmara de sal Q-Fog, conforme os padrões estabelecidos pela ASTM B117, e posteriormente analisada segundo a ASTM D610 para determinar o grau de corrosão. Todos os revestimentos foram aplicados em parafusos e porcas sextavadas frequentemente utilizados em ambientes industriais marinhos.
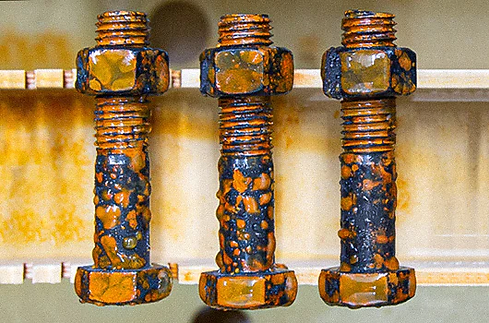
Resultados em 48h
Após 48 horas de análise, ambos os tipos de Teflon® ultrapassaram o padrão de falha de 3% no corpo dos parafusos. Os parafusos de Teflon® foram retirados da câmara em 640 horas com 100% de corrosão.

Resultados em 530h
Os parafusos Xylan® atingiram o padrão de falha de 3% em 530 horas na câmara. As foram removidas da câmara em 1.871 horas com aproximadamente 60% de corrosão.

Resultados em 3963h
Por outro lado, em 3.963 horas, os parafusos Cerakote® Blackout não tinham atingido o padrão de falha.
CONCLUSÃO FINAL
O teste foi concluído às 4.008 horas, pois o Cerakote Blackout ainda não havia atingido o padrão de falha de 3%. A análise dos dados derivados do Cerakote Blackout proporcionou uma melhoria de 99% em relação ao Teflon® e uma melhoria de 87% em relação ao Xylan® na resistência à corrosão.
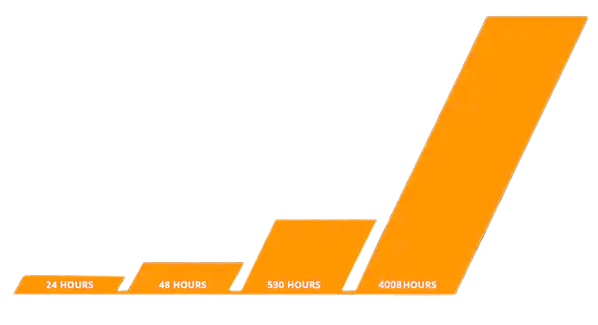
Garanta a melhor proteção do mercado para suas peças!
bottom of page